is part of the Informa Markets Division of Informa PLC
This site is operated by a business or businesses owned by Informa PLC and all copyright resides with them. Informa PLC's registered office is 5 Howick Place, London SW1P 1WG. Registered in England and Wales. Number 8860726. Spindle Cnc Router
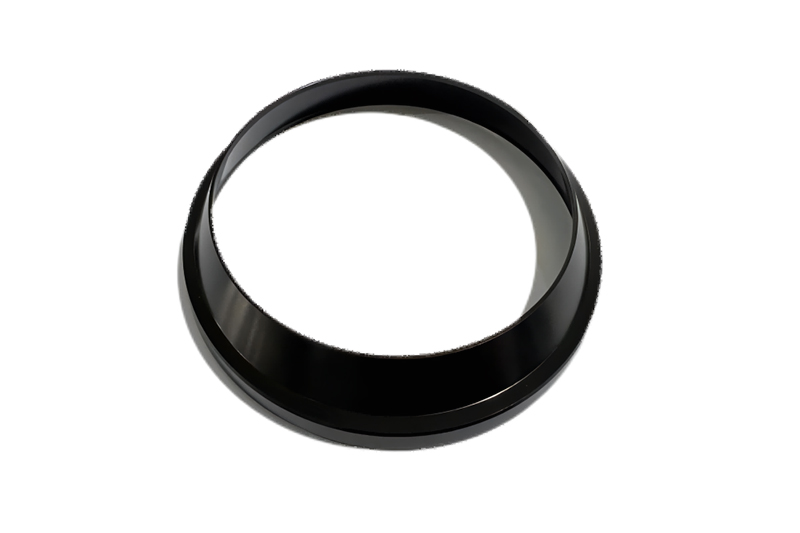
Many facets affect a company’s ability to achieve high injection molding production numbers while maintaining low scrap and minimal unplanned down time. One of the largest factors is the machine itself. There is much debate over which OEM produces the best press, but at the end of the day it is the planning and research conducted prior to purchasing a machine that will make the biggest difference. This article will delve into what needs to be taken into consideration before purchasing a press.
New or used? Many larger companies will purchase only new equipment and replace it every five to seven years with another new press. The strategy is to avoid unplanned maintenance at all costs. This system can be quite effective if the company is producing premium parts that generate high margins. For a smaller molding operation, however, the cost of new machinery may put this approach out of reach. If used machines are the best option, it is highly recommended that presses be no more than 10 years old. Also, the buyer should make every effort to get a sense of how the seller dealt with preventive maintenance.
Press controller. The controller is a huge consideration when choosing a press. If your processing requirements are complex, the controller will need to have adequate functionality to accomplish the processing capabilities needed for minimal scrap and high productivity. Keba and Mosaic controllers are among my favorites, but there are several other controllers that can rival their dependability and technical applications.
Hydraulic, electric, or hybrid? Which of these three systems is the most reliable is debatable, but the fact is that each one has its pros and cons. Hydraulic presses continue to be a solid contender, but they can be messy and require greater maintenance. Electric presses are cleaner and need less maintenance but they can sometimes struggle with higher pressure process applications. Hybrids are just a combination of hydraulic and electric systems and, thus, combine the pros of both systems. It is recommended that a company first determine the type of molding operation it intends to use. High-tolerance molding is best served by electric presses, which hold more exact tolerances and are best suited for medical, aerospace, and high-tech automotive applications. Hydraulic presses, on the other hand, are more cost efficient.
Screw and barrel. When planning a machine purchase, the importance of screw and barrel evaluations can’t be overstated. Understanding what molds you will be running in a press will define the screw throughput requirements. Materials that spend too much time in a barrel are prone to degradation and splay. Shot sizes that are too large for barrel throughput will inhibit your ability to run some molds in a press. Call on the expertise of your materials and screw suppliers to ensure that screw and barrel functionality will meet your needs.
Clamping system. Clamp requirements are a crucial decision when buying a press. What are your mold thickness requirements? What is the size of your largest mold, and will you be able to mount it to the platen? What is your maximum tonnage requirement? These measurements and setpoints are important to the press design needed to produce parts in your facility.
Auxiliary functions: Any extra bells and whistles you want on the machine should be the final consideration. How many cores do you expect to need? Will the hot runner be built into the main controller? Will mold temperature be a main controller function? Will you be using valve gates, and will they be part of the main controller function?
Every plastic injection press in your plant must adequately achieve productivity and final yields after scrap to make your operation successful. Take time to determine all press requirements prior to making the final decision to purchase. This ensures an end result of high profitability, which is key to any company’s success.
Got a problem with this, that, or the other thing? You might find answers in some previous "Troubleshooter" columns:
How to Identify and Correct Shear-Related Splay Defects
The Role of Moisture in Injection Molding Splay Defects
Preventing Flash in Injection Molded Parts
How to Prevent Common Failure Modes in Injection Molding
Building a Validated Plastic Injection Molding Process
Fixing Color Defects in Injection Molded Parts
Key Steps for a Stable Injection Molding Process
Fundamentals of an Injection Molding Plant or Cell Startup
Garrett MacKenzie is the owner/editor of plastic411.com and a consultant/trainer in plastic injection molding. He has provided process-engineering expertise to many top companies, including Glock, Honda, Johnson Controls, and Rubbermaid. MacKenzie also owns Plastic411 Services, which provides maintenance and training support to Yanfeng Automotive Interior Systems, IAC, Flex-N-Gate, and other top automotive suppliers. He was inducted into the Plastic Pioneers Association (PPA) in 2019, where he serves on the Education Committee evaluating applications from college students seeking PPA scholarships. You can reach him via e-mail at [email protected] .
More information about text formats
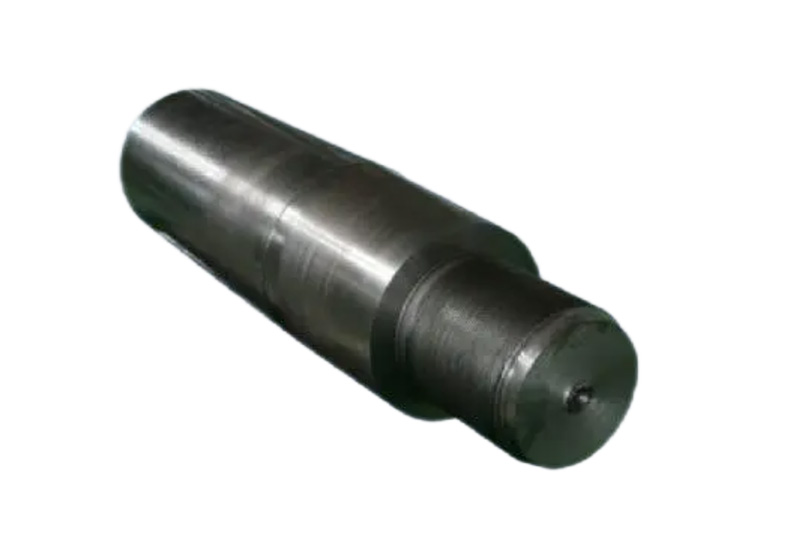
Plastic Molded Check out our coverage of mind-blowing new plastics applications and more.